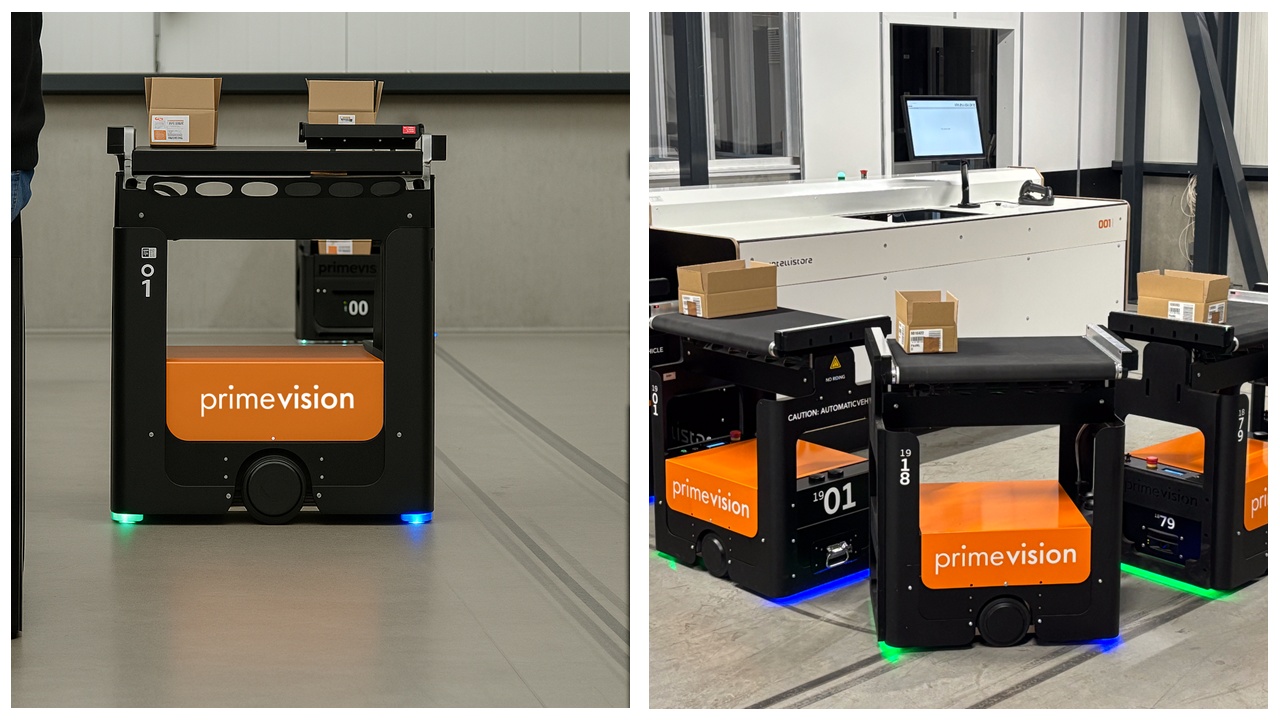
Prime Vision is giving businesses the opportunity to sort orders in an efficient and scalable manner.
This is certainly the case for K-Parts, a leading online supplier of scooter, moped, motorbike and bicycle parts, which is using Prime Vision robots to accelerate its warehouse logistics at Harderwijk in the Netherlands. Working together with K-Parts staff and an automatic storage and retrieval system (ASRS), robots have optimised the sorting process and powered future growth.
A web shop for anything on two wheels, K-Parts offers bikers seamless access to a wide range of high-quality parts to keep their pride and joy on the road. As the business grew, operators at its warehouse identified the need to automate its order picking process to improve efficiency and profitability. This wasn’t straightforward, as spare parts vary greatly in size and shape, making process automation challenging.
K-Parts has replaced its original manual order picking process with an ASRS. When a web shop order is received, a custom box is erected that corresponds to the total volume of the products specified. Then, the box is transported to the right picking station, where K-Parts staff pack the box with items provided by the ASRS. With this complete, the full box goes to the box closing machine, ready for sorting to the correct delivery destination. Now fully operational, the system has reduced waste, lowered manual intervention and improved efficiency.
However, when designing the system, the question was how to transport the boxes and items between the different process steps? Considering the typical volume of 365 orders an hour, as well as the limited space within the application area, using conveyors didn’t make sense. Instead, K-Parts needed a highly flexible solution that could work efficiently in a small footprint, so the company approached Prime Vision to provide a fleet of robots to complete the task.
Standing at 875mm tall with an 80 x 60 cm loading surface ready to transport small or large items weighing over 30 kg, Prime Vision robots offer the versatility to carry a wide range of box sizes – making them highly suitable for K-Parts’ requirements. Totally autonomous thanks to uploaded maps of the facility and route data for the other robots from the overarching fleet management system. These robots can drive to and from any destination within a sorting centre, using information from the warehouse management system to move items to the right place. This allows them to transport small, medium or high volumes incredibly efficiently within a much smaller footprint than conveyors.
Prime Vision Account Director, Richard Hagen, explains further: “We have supplied a fleet of eight robots to move between the box erector and three picking stations. Due to each box being custom-made for a specific order, it was important that items and corresponding boxes arrived at the right picking station in perfect sequence. This was a key reason why robots were preferred, as boxes can be directed to the right station and queued up until it’s time to pack them with the correct products.”
“Other factors were a fire door in the application area and the positioning of the infeed conveyor providing the boxes. The robots use live data to plot a safe, efficient route to enable them to receive parcels without causing an obstruction. The robots have sensors fitted to detect any overhangs over the conveyor, which helps to load boxes of different sizes.”
While the system is optimised for current volumes, scalability can be achieved by adding or removing robots from the existing fleet. Adding a new order picking, pick-up or drop-off point is simply a case of adding it to the facility map, which will enable the robots to drive themselves to the location. Increasing the capacity or complexity of the order picking operation is relatively straightforward, allowing peak times to be serviced more effectively.
“With bike parts, order volumes increase when the weather improves and bikers get on the road, then on Monday on Tuesday after any weekend breakdowns. The efficiency, flexibility and scalability of robots mean that these peak times can be serviced effectively without placing undue strain on staff. More orders can be fulfilled with less people,” Richard explains.
Bram van Eikenhorst, Operations Manager at K-Parts adds: “The advantage of us partnering with Prime Vision is that we are optimising our resources to maximise productivity. Ordered items and the corresponding box are conveyed quickly to sorting staff, they never have to search for anything. Our order picking process is very effective and never stands still, saving us a lot of manual labour, costs and time. I would absolutely recommend Prime Vision, especially for people who are in a similar situation to us.”
Along with the robots, Prime Vision has provided charging stations as well as a preconfigured spare unit to safeguard uptime should a breakdown occur. Prime Vision handled the full integration of the robots. K-Parts also benefits from 24/7 maintenance support, with Prime Vision able to handle 90% of issues remotely.
Richard says: “Robotic sorting is a compelling solution as it allows any operation handling more than 800 items a day to cost-effectively automate even the most complex sorting processes. This makes it accessible to and profitable for growing e-commerce organisations, where improving efficiency is essential for maintaining this trajectory. We support thousands of systems for over 50 customers globally, so this is something we’re very experienced in.”
Bram van Eikenhorst at K-Parts concludes: “Working with Prime Vision robots helps us by providing the flexibility and dynamism that our fulfilment processes require. We are a growing company, and these robots will keep our service consistent during high demand.”
Watch the process of Robotic Sorting at K-Parts here: https://www.youtube.com/Robotic_Sorting_at_K-Parts
https://couriernews.co.uk/blog/prime-vision-robots-optimised-for-k-parts/